Infrared Emitters Allow Heating Processes To Be Automated
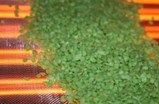
Corrosion protection on large metal components, clear varnish on plastic products, coloured décor on stone – different coatings need to be dried on a large number of different products. Infrared systems help to ensure that the heating steps required for drying are carried out as efficiently as possible.
In the "Surface Technology in Practice" area of the Hannover Fair, which takes place from 4th to 8th April, Heraeus Noblelight will be presenting its infrared emitters on Stand J34 in Hall 6, where visitors will also have the opportunity to meet with application specialists.
Small, irregularly shaped stones or other bulk materials are dried just as reliably as large surface metal parts using infrared heating technology. In both cases it is vital that the heating source is exactly matched to the product and the process. It is often worthwhile to put the complete system on the test bench to increase output and minimise energy consumption.
Metal plates must be heated homogenously over the complete surface to guarantee the quality of the coating. A precisely matched emitter arrangement in combination with a suitable control system brings significant improvements.
Using a suitable guidance system into the system, which ensures the optimum alignment of stones or granules to the radiation, bulk materials can be dried significantly more efficiently.
Drying of Coatings
No coating process is exactly the same as another but with all processes it is important that the lacquers and paints should be dried to high quality and as quickly as possible.
Many coatings set challenges which cannot be met with standard heat sources. The coating system defines the data framework. Water evaporates more slowly than solvents, so that infrared emitters dry water-based lacquers significantly faster because they are optimally matched to the absorption properties of water.
Nano coatings to some extent require very high temperatures, which can be reliably delivered by infrared emitters. Powder coatings must be gelled very quickly and it saves time and money if only coating and surface are heated. The products are then ready for further processing much more quickly after the heating stage.
Optimising the System Saves Energy
The drying of lacquers and coatings increasingly needs to be faster but at the same time, drying must produce a top quality product and use the minimum amount of energy. The reduction of energy and material costs is very important to industrial companies in their struggle to maintain or improve competitiveness. Often it is more sensible and cost-effective to optimise an existing system rather than introduce new plant. A newly formed consulting team at Heraeus Noblelight offers support here through individual consultancy, practical planning and the prompt implementation of measures to optimise systems and processes.
Energy Efficiency Through Precise Matching Infrared heating technology offers several possibilities of optimising energy consumption in industrial heating processes:
- High heat transfer capacity
- Contact-free heat transfer
- High efficiency
- Efficient energy transfer through the use of optimum wavelengths
- Energy usage confined to the working area by matching to the product shape
- Energy used only when required because of fast response times
Infrared heat will always be used whenever heating processes with particular challenges in terms of space, time or quality need to be resolved. Infrared emitters can be precisely matched to product and process and this saves energy and costs.
SOURCE: Heraeus Noblelight GmbH