Multi-Axis Conformal Coating Machine Handles High Volume Throughput
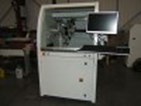
Baldor Ethernet-compatible Powerlink servos simplify machine build
An advanced real-time Ethernet motion control system has helped Advanced Coating Robotics (ACR) to create a new conformal coating machine that combines exceptional three-dimensional spraying accuracy with very high throughput.
The multi-axis system is based entirely on Baldor Electric motion control products, with three axes making use of the company's Ethernet-compatible PowerLink servo drives. Key reasons behind the choice of this motion control technology were the flexibility of Baldor's motion control software, the ease with which real-time interpolated control could be applied across the machine's five-axis servo and stepper driven motion, and the simple plug-together system building approach offered by the Ethernet-based modules.
ACR's new MACCS 400 machine provides a fast and highly flexible means of selectively applying protective conformal coatings to printed circuit board (PCB) mounted components, and can accommodate both inline and batch processing operations. Capable of coating PCBs as large as 500 x 480 mm - with on-board components as high as 90 mm - the programmable machine uses an advanced five-axis motion control system to combine high-speed throughput capabilities with ultra-precise spray head positioning to an accuracy of 25 microns.
Formed in 2009, with the specific intention of developing highly automated solutions for applying conformal coatings to electronic components, ACR is a collaboration between SCH Technologies - a leading conformal coating company - and specialist automation designers SMS Machines & Automation Ltd. ACR launched the MACCS 400 just three months ago and has already sold five of the machines.
MACCS 400 is a self-contained, free-standing machine with a small 1.4 m2 footprint. It is capable of completely autonomous operation, or can be equipped with chain conveyors and form part of an integrated PCB production line; the machine is fully compliant with the SMEMA (surface mount equipment manufacturers association) mechanical and electrical interface standards.
The X and Y axes of the machine's motion control system are based on a novel 'H-belt' actuator, driven by two Baldor BSM servomotors linked to Baldor MicroFlex e100 drives. The two motors are static - they occupy fixed positions at the bottom of the 'H' - and jointly act on a single belt. The advantage of this approach is that the motors do not contribute to the load inertia, and therefore permit very fast and accurate movement - the machine can accommodate X-Y velocities as high as 800 mm/second. The Z axis controls the above-board height of the spray head, and is driven by a third BSM servomotor and MicroFlex e100 drive. All three drives are very tightly synchronised to facilitate high speed Cartesian movement of the spray head, the angle and orientation of which are controlled by two rotary axes, driven by Baldor stepper motors.
All five electrical axes on the MACCS 400 are controlled by a Baldor NextMove e100 controller, using full interpolation to allow smooth high speed tangential moves. Overall control of the machine is handled by ACR's proprietary coating software, which runs under Windows XP on a built-in host PC, equipped with a large HMI (human-machine interface). The coating software provides a highly intuitive graphical user interface and is written in the VB.NET object-oriented programming language.
According to ACR's Managing Director, Gordon Watson, "Our choice of motion control technology was heavily influenced by the flexibility of Baldor's NextMove controller, which interfaces seamlessly with our software. Baldor's software development environment, which comes as part of the package, includes comprehensive support for ActiveX, which fits well with VB.NET. Creating the complex real-time motion control sequences was also relatively easy, since Baldor's Mint language employs high level keywords for many of these moves. And since taking the decision to adopt Baldor as our supplier of choice, we have been extremely pleased with the excellent level of application support that the company provides."
The MACCS 400 can apply a wide range of conformal coatings, including Parylene and many HumiSeal products, and offers a choice of cartridge or pressure vessel feed. Standard features include an integral camera for manual alignment, a remote teach pendant, and built-in purge and solvent cups for flushing. The machine also offers numerous optional facilities, such as multiple spray heads, fluid viscosity control, a bar code reader and a laser pointer.
SOURCE: Wordsun