Diamond Lapping Is The Process Of Choice For Finishing Ceramic Surfaces To Precise Dimensions, Finish Requirements
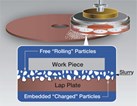
An article in the May 2011 issue of Ceramics Industry magazine provides an overview of the flat lapping process, highlights case studies showcasing the advantages of diamond over conventional abrasives and provides best practice guidelines for achieving consistent diamond lapping results on advanced ceramics.
Wheeling, IL (PRWEB) - Engis Corporation's Mark Irvin, an expert on superabrasive finishing solutions, has authored an article on page 24 in the May issue of Ceramics Industry magazine that details why diamond lapping is the most appropriate process for finishing ceramic when faced with specific challenges.
These challenges include working with non-oxide advanced ceramics or dense, high purity oxide ceramics; greater planar, spherical or conical surface requirements; improved sealing or cosmetic surfaces; planarizing joined dissimilar materials (e.g., laminates, composites); surface deburring or removal of "gummy" materials and thinning/finishing poor aspect ratio parts.
Common applications for flat lapping of precision ceramics include mechanical seals, seal rings, pump parts, vacuum chucks, fixture components, wafers for micro electro-mechanical devices (MEMs) and flat glass or mirror substrate. Almost any application of engineered ceramics, where demanding requirements exist for flatness and/or surface finish, may benefit from the diamond lapping process.
The article compares diamond lapping to lapping with conventional abrasives, provides case study results and shows how diamond lapping can offer the following benefits:
- Aggressive material removal for equal or better productivity.
- Uniform edge-to-edge flatness. Sub-light band (11 millionths inch) results are routine; up to 1/20 wavelength is achievable under specific conditions.
- Better than sub-micron surface finish (< 0.5 Ra) is routine; sub-nanometer surface finishes are achievable.
- High potential to develop a one-step lapping and polishing solution for reduced cycle times.
- Reduced waste to support green initiatives.
To learn more, read the entire article on CeramicsIndustry.com site, or visit http://www.engis.com for addition information on superabrasive finishing solutions.
Engis Corporation, headquartered in Wheeling, Ill., is a leading worldwide provider of superabrasive finishing systems and HYPREZ® high precision micron diamond and CBN powders. Engis solutions include grinding, honing, lapping and polishing products, as well as fully configured, custom-developed manufacturing systems. Industries served include oil & gas, electronics, semi-conductor, medical devices, aerospace, defense, ceramics, mold/tool/die, automotive, mechanical valves/seals, foundries and more. A privately held company, Engis employs approximately 140 people in Illinois and 200 worldwide, which includes five locations in Asia, one in Europe and one in Canada.
For more information, visit Engis' Web site at http://www.Engis.com or call 800-993-6447 or +1-847-808-9400, e-mail info(at)engis(dot)com, fax +1-847-808-9403 or write to Engis Corporation, 105 West Hintz Road, Wheeling, IL, 60090.
SOURCE: PRWeb
View original release here: http://www.prweb.com/releases/2011/5/prweb8487673.htm