Increasing Seal Face Capability In Hard-On-Hard Combinations
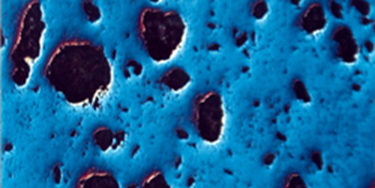
As operating conditions become more severe, hard-face materials must continue to efficiently rub against each other to maximize their inherent benefits. iAbrasive report.
Zhengzhou, China (PRWEB) - The composition and design of mating faces in contacting mechanical seals are critical in preventing the media on one side of the face from successfully reaching the other. Different materials are employed, including mechanical carbon-graphite with resin or antimony impregnation, metals and hard coatings,aluminum oxide, tungsten carbide, and silicon carbide.
The latter three “hard face” materials are often used in particularly challenging applications, where they are in contact with each other. As operating conditions become more severe, hard-face materials must continue to efficiently rub against each other to maximize their inherent benefits. Unlike mechanical carbon-graphite, these hard-face materials are not self-lubricating and so are unable to function for extended periods of time without fluid lubrication. Other enhancements therefore need to be made to extend the capability of the hard-face mating pair.
Silicon carbide is hard and has excellent abrasion and wear resistance. It has a low coefficient of friction when lubrication is available, high hardness and high modulus of elasticity. It also retains its strength at elevated temperatures, has a low thermal expansion coefficient, high thermal conductivity and excellent corrosion resistance.
In the 1970’s, Chemical Vapour Reacted (CVR) silicon carbide demonstrated an enhancement for contacting seal faces. The porous outer surface encapsulates a carbon graphite core and provides a hardened surface with a unique topography for increased interfacial lubrication.
Sintered silicon carbide can be formed into specific shapes and then sintered to, or nearly to, the finished size, limiting the amount of expensive grinding for the finished item.
Silicon carbide materials now often have the form of a two-phase composite applied in the highest duty applications, the most popular being silicon carbide and graphite. These composites are often referred to as “graphite-loaded” silicon carbide since the graphite is integrated (not impregnated) into the silicon carbide structure.
The graphite creates small reservoirs on the surface that provide a controlled texture for lubrication without creating leak paths. This texture increases the hard face combination’s ability to operate under more rigorous pressure and velocity (PV) conditions.
This unique family of composite materials has the benefits of sintered silicon carbide while incorporating a second, abradable phase that provides pockets or reservoirs for the "storage" of fluid.
Diamond is the hardest material with excellent tribological behavior, heat conductivity and chemical resistance. These qualities are produced on the surface of a conventional finished silicon carbide ring by growing a crystalline diamond film on the surface. This is created by placing the silicon carbide ring in a chamber where the pressure, gas composition and temperature are accurately controlled. A carbon bearing gas such as methane (CH4) is introduced and, under the right processing conditions, diamond crystals grow on the silicon carbide.
Composite graphite-loaded silicon carbides have been developed with graphite integrated into their structure which creates small reservoirs on the seal face surface that provide a controlled surface for lubrication without creating leak paths. The integrated graphite extends throughout the material, producing an enhanced capability throughout the life of the components. It is also possible to control the quantity and particle size of the graphite in the structure for a given application.
Graphite-loaded silicon carbide materials enable greater reliability for hard-on-hard seal face material combinations. Not all graphite-loaded composites are the same - the second phase's integration is as critical as its presence in the matrix. The presence of the second phase reduces key characteristics of the material, potentially limiting its use in some of the highest mechanically loaded conditions. This limitation has led to the development of a hybrid silicon carbide.
Hybrid composite silicon carbide improves and sustains the physical characteristics of the homogeneous silicon carbide in the bulk of the material while incorporating the benefits of the graphite addition only on the seal face itself. The integration of the two-phase composite texture onto a homogeneous substrate provides the physical attributes of the bulk silicon carbide and the tribological enhancement of the composite (patent pending).
This development allows the structure of the composite graphite-loaded silicon carbide to be customized for a given application, creating an ability to tailor the seal interface for demanding requirements without affecting the physical strength or other attributes of the material.
iAbrasive, established in 2013, headquartered in Zhengzhou, China, is a leading abrasive and diamond tools trading platform, through which overseas buyers can get in touch with chinese manufacturers and be informed of the lastest news about abrasives and abrasive tools industry.
For more information, please visit: http://www.iabrasive.com/
Source: PRWeb
View original release here: http://www.prweb.com/releases/2014/04/prweb11772470.htm